
Hand safety at Greenhams
Injury to hands is a major component of all workplace injuries and can be a costly.
The first report on hand injuries in Australian workplaces, “In Safe Hands: The State of Hand Protection in Australia 2016”, reveals more than one-third of Australian companies are unaware of how much hand injuries are costing their business.
The independent research into hand injury rates, reporting and management practices in Australia highlighted that only 28% of employers track hand injury costs and 48% have only a partial picture of the full cost of hand injuries.
The research was undertaken in response to the Australian safety community’s need for benchmarking data about safety performance and best practices within the Australian Occupational Health and Safety (OHS)/ Work Health and Safety (WHS) industry. The independent research company AMR carried out the survey in conjunction with the National Safety Council of Australia Foundation (NSCA) and Ansell.
A survey was carried out across 17 different industries. It included small employers of 24 people to organisations with more than 100 employees. The objectives were to evaluate current safety practices and procedures; the measurement and rating of hand injuries; cost of hand injuries and a review of which best practices have been implemented.
AMR collected data over five months and interviewed more than 200 members of the Australian safety community.
Key findings emerged as a result of the survey –
- 73% of organisations indicated safety performance has improved year-on-year.
- safety leaders rated cultural initiatives as more useful or successful than technical or PPE (personal protective equipment) improving safety performance,
- 75% of organisations measured lagging indicators such as LTIs (complete day or shift time loss) and MTIs (medical treatment injuries) and other lost time, while 73% measure leading indicators such as training hours and near hit reports,
- 93% of organisations reported injuries to hands, with cuts (64%) abrasion (44% and impact (42%) being the most common.
Responses clearly showed an ongoing debate between leading versus lagging indicators when comparing management mandates for safety equipment compared to a mentoring approach. Many respondents pointed to time constraints, reduced resources and cost-cutting by management as the primary challenge in managing safety.
Commenting on the findings of the report, Jamie Burrage, NSCA General Manager noted the value placed on an effective safety culture and employee engagement through coaching and mentoring, rather than a top-down prescriptive approach to safety at work.
“Many respondents identified the emerging new practice of mentoring to influence behavioural change as less useful. There appears to be a conflict in how senior management views the effectiveness of mentoring compared to the view of other management levels and workers,” he said.
Ansell Marketing Manager, Dean Clark, said the report highlights the difficulty faced by safety leaders in building safety performance and compliance that meets their commercial obligations when they don’t have a complete picture of the cost of injuries.
“Comments from respondents show significant differences in the level of understanding about the true cost of injury to businesses. When you consider the research was conducted across industries where safety is a key consideration, this shows a need for better education in addressing the costs of hand injuries by taking into account measuring costs of treatment, workers compensation, loss of productivity, re-training and insurance premiums,” Mr Clark said.
Hand safety and the meat industry
The report is a timely reminder for the meat industry on the importance of hand injury safety. The initial survey however, did not include representatives of the meat industry, but the findings can be readily applied.
Current statistics of hand injury in the workplace shows that it is still a major source of lost time and compensation in the meat industry. A spokesman from WorkSafe Victoria said that, “over the past five years, there have been more than 330 hand injuries in the meat sector (Victoria) serious enough for a workers’ compensation claim to be made. While the number of hand injuries is slowly declining, last year there were still almost 60. No injury at work is acceptable and employers need to do more to keep their employees safe.”
Complete details of the survey and outcomes are available in the report titled “In Safe Hands: The State of Hand Protection in Australia 2016” is available for download at ppp.ansell.com.au/handsafetyreport.
The importance of a sharp knife at home and at work
Most people keep a handful of kitchen knives in their cutlery drawer and never sharpen them from the day they are purchased. The key to safety whether you are a butcher or doing home food preparation is the same. Luke Benjamin of Total Knife Care has three reasons for keeping your knife sharp:
- Safety: Sharp knives are safer than blunt ones. Many injuries in food preparation are caused by blunt knives requiring more pressure to cut – it’s when the knife slips that people get hurt. If you’re using knives all day, that extra pressure you need to use a blunt knife can cause RSI – Repetitive Strain Injury. A small cut from a sharp blade will generally heal more quickly, as microscopic nicks in a blunt blade harbour more bacteria.
- Speed: It simply takes longer to prepare food with a blunt knife – a professional kitchen runs ‘as fast as the bluntest blade in the room’.
- Presentation: Whatever food you are preparing – meat, fish or vegetables, you need it to present well. You are not going to get beautiful and delicious looking food with a blunt knife.
In the past, to keep knives sharp you needed to spend half an hour or more using a whetstone for each knife. A good quality electric knife sharpener does the same job to the same standard in a fraction of the time.
Greenhams : You must wear gloves . . .
H W Greenham & Sons in central Victoria has a mandatory glove policy requiring a range of glove types depending on the application. The facility processes and exports ground beef for the US Burger King restaurant chain and employs 230 staff, all of whom are required to wear some form of specialised PPE.
“Relatively minor cut injuries that affect workers and productivity is a common problem in this industry, so everyone is looking for solutions that can reduce or eliminate these injuries”, said Operations Manager Darren Maloney, H W Greenhams.
“Our mandatory glove policy means that workers are unable to remove gloves to perform any task and involves disciplinary action should any operator remove gloves for any reason while on the job,” Mr Maloney said.
“Every part of the process involves workers cutting meat from bone and is therefore a dangerous procedure. Very sharp knives are used in almost every stage of production and this is the reason why everybody is required to use hand protection.
“Cut injuries that often required one or two surgical stitches, resulting in absenteeism and adversely impacting production was the catalyst for a glove evaluation that was led by our OH&S committee in conjunction with our abattoir workers.
“The Committee trialed several different styles and makes of cut-resistant gloves in their quest for protection that would deliver comfort and dexterity, as well as the key requirement of high level cut resistance. The prime need was for a glove to be worn as an under-glove to provide the final barrier between potential knife injury and an operator’s skin.”
Greenham’s chose to go with Ansell’s polar bear cut resistant gloves that provided a high level of cut resistance, while the feel and comfort of the material enabled staff to carry out their work efficiently. A strict laundering process maintains the required level of hygiene for the US FDA.
“Investment in appropriate hand protection pays dividends in terms of worker wellbeing, minimizing downtime, maintaining productivity and controlling workers compensation premiums. Furthermore, our work environment is very tough on gloves and as we get around three months wear out of each pair of Ansell polar bear cut resistant gloves, this helps us budget our hand protection costs more accurately,” Mr Maloney concluded.
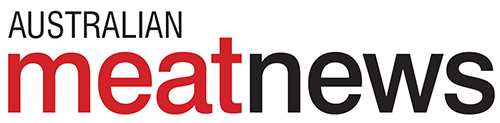
Published by Optimal Media
Australian Meat News
PO Box 415
Richmond Victoria 3121
T 1800 621 631
athol@ausmeatnews.com.au
Sign up to our newsletter for all the latest from Australian Meat News
COPYRIGHT Editorial and advertisements may not be reproduced without the written consent of Optimal Media. While every effort is taken to ensure content accuracy, Optimal Media does not accept any responsibility or liability for material herein.